News
Stronger steel bonds thanks to neutron imaging

Bonding steel pieces
Steel is the backbone of infrastructure and technology, from skyscrapers to engines. However, joining steel components has always been a challenge. Traditional welding processes – like brazing – often leave inconsistent material properties at the joints, which can compromise the strength and performance of the final product. This is particularly problematic in critical applications where every fraction of strength matters.
To address this, scientists from the Laboratorio de Sólidos Amorfos, INTECIN, Facultad de Ingeniería (UBA-CONICET), the Heinz Maier-Leibnitz Zentrum (MLZ), and further institutions turned to a method called transient liquid phase bonding (TLPB). This technique uses a special filler material—in this case, thin metallic foils made of iron and boron (Fe-B)—to bond steel pieces at high temperatures. As the materials cool, the connection is formed. However, to make this process work effectively, researchers needed to study and control how the boron spreads throughout the joint.
Peering inside steel bonds
This is where ANTARES, a cutting-edge neutron imaging facility at the MLZ, played a crucial role. Unlike X-rays, which are better suited for superficial studies, neutron radiography is perfectly suited for volumetric studies. Dr. Michael Schulz, deputy scientific director, leading instrument scientist at ANTARES and co-author of the research paper, explained: “By sending a focused beam of neutrons through the steel samples, we have the unique possibility of measuring the concentration of boron within the steel joint with high accuracy and spatial resolution, without destroying it.”
The neutron images revealed a uniform spread of boron across the joint, with only a small, localized concentration in the centre. This balance was critical—it ensured that the joint remained strong and avoided the formation of brittle compounds called borides that could weaken the bond. With this insight, the researchers confirmed that their process created a connection as strong and ductile as the original steel.
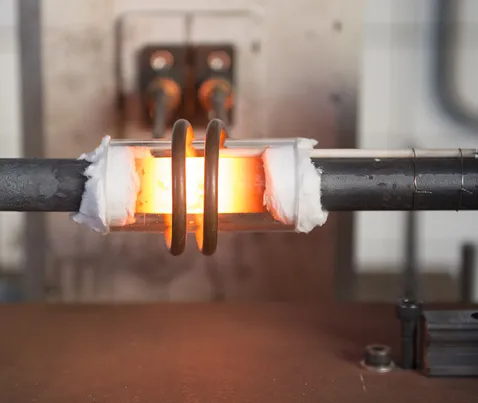
Applications in the oil and gas industry
This advance in diffusion bonding technology opens the door to numerous applications where strong steel joints are essential. For example, the oil and gas industry is still relying on threaded pipes in upstream operations—that is to say, inside the well. Flush steel bonds can endure extreme stresses without failing, outperforming flush threaded connections.
Similarly, in the automotive sector, diffusion bonding could enable new designs, where lightweight and durable parts are key to improving fuel efficiency and vehicle performance.
Reducing costs
Dr. Nicolás Di Luozzo highlights another exciting application in advanced heat exchangers: “Printed circuit heat exchangers can be produced using TLPB instead of solid-state diffusion bonding, leading to significant cost reductions without sacrificing quality.” These heat exchangers are used to transfer heat in demanding applications, such as natural gas processing, hydrogen production, and chemical processing plants. They must handle extreme temperatures and pressures, making strong and reliable joints crucial for their performance.
By ensuring that steel bonds are as strong as the rest of the material, this technology has the potential to lead to safer, more efficient, and longer-lasting structures and machines.
Original publication:
Nicolás Di Luozzo, Michael Schulz, Michel Boudard, Silvina Limandri, Gastón Garbarino, Marcelo Fontana,
Diffusion bonding of steels with a homogeneous microstructure throughout the joint
Metals & corrosion, 59, 20400 (2024)
DOI: https://doi.org/10.1007/s10853-024-10343-x
Partners of the project:
Laboratorio de Sólidos Amorfos, INTECIN, Facultad de Ingeniería (UBA-CONICET), the Heinz Maier-Leibnitz Zentrum (MLZ), Université Grenoble Alpes, the Instituto de Física Enrique Gaviola, UNC-CONICET, and the European Synchrotron Radiation Facility.